Hier ein kleines Update zum Stand der Technik. Viele Weisheiten alter Hasen beruhen auf den Gerüchten der letzten 30 Jahre :-) Leider halten sich auch diese hartnäckig, der Stand der Technik verändert sich aber stetig.
Viele haben vielleicht noch die Pflichtlektüre des Ludwig Apfelbeck zur Hand. Da liest man auch viel Interessantes. Manches hat sich relativiert, viele seiner innovativen Konstruktionen waren aufgrund damals schlechter Materialien oder begrenzter Fertigungsmöglichkeiten absolut nötig. Wenn man bedenkt, dass Ludwig Apfelbeck von 1903 bis 1987 gelebt hat, also bis zum Höhepunkt der Entwicklung der KFZ Technik (seitdem geht es mit der Qualität und den Innovationen bergab), versteht man, warum er bei Pleuel z.B. beschreibt, dass diese nicht aus dem Vollen gearbeitet werden können, da zu aufwendig. In den 80'er erfolgte die flächendeckende Herstellung von CNC Werkzeugmaschinen, inzwischen ist es Stand der Technik, dass Pleuel in Kleinserien spezifisch für Einzelstücke aus dem Vollen mit einer CNC Fräse hergestellt werden. Das Gleiche auch bei Kolben.
Kein Wunder also bei der modernen Fertigungstechnik, dass jeder Tuningmotor bessere Bauteile hat, als ein Formel 1 Rennwagen Motor in den 70'ern. 200 PS Literleistung (im Turbobereich) sind im Alltag möglich, wenn auch nicht bei allen standfest. Die Deutschen wollen es nicht hören, aber nur die Toyota (Yamaha) Motoren und alten Nissan 4 Zylinder und Nissan V6 Motoren sind für Höchstleistungen konstruiert. Der letzte gute Audi Serienmotor war der 1.8l 5-Ventilmotor, der lange in allen 1.8T Modellen zuverlässig als Basis diente. Die Blockkonstruktion wurde übrigens für die nachfolgenden 2l Motoren weiterentwickelt. BMW Motoren sind nicht mehr vollasttauglich und gehen schon auf Prüfständen reihenweise in die Luft. Die mangelhaften VW Konstruktionen mit reihenweise Motorschäden wegen unterdimensionierter Bauteilauslegung ist ja weitläufig bekannt. Selbst der "legendäre" Ur-GTI mit knapp 70 PS Literleistung hielt nahezu keine 100.000km und war eigentlich die gleiche Krücke, wie der Käfer. Besagter 1.8T verträgt auf 300PS getunt 700km Dauervollgas ohne Schäden, soweit Öl- und Wasserkühlung ausreichend dimensioniert. Stand 2020 ist bei Premium Herstellern die Auslegung auf 160000km und 4 Jahren. Danach sind nahezu alle Motoren abgenutzt, egal ob 80000 Euro oder teurer. Unterdimensionierte Ölversorgung und keine Öldrucküberwachung und aus Emissionsgründen sehr dünne Öle sorgen bei vielen Mercedes und den BMW 6-Zylindern für massive Motorschäden. Bei VW Motoren standard, defekte Hydrostössel nach 70000km, egal wie gut man die Motoren pflegt und wie gut das verwendete Öl ist.
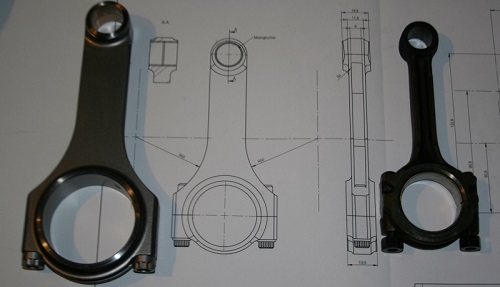
Links Carillo H-Schaftpleuel für 2,2l PSA Motor (300PS), mitte Konstruktion Nissan CG13DE H-Schaftpleuel (150 PS), rechts geschmiedete Nissan Serienpleuel für ca. 7500 1/min Dauerdrehzahl.
Materialien
Serienpleuel unterliegen immer dem Kostendruck. Es werden die billigsten Fertigungsverfahren bevorzugt. Ist ein Pleuel um 5 Cent billiger und hält statt 8500 1/min für 500.000km nur 6500 1/min für 500.000km dann verwendet die Autoindustrie das 5 Cent billigere, auch wenn die Nenndrehzahl 6500 1/min beträgt. Was Porsche oder BMW in der Serie einsetzte mag funktionieren, ist aber nicht das technische Optimum: gesinterte/gecrackte Pleuel. In den 70'ern baute Porsche noch Titanpleuel in seine Motoren ein...
Großserienpleuel werden geschmiedet oder gesintert. Ein Indiz für Sinterpleuel ist ein gecracktes Pleuel. Auch ein spezielles C70S6 (schwefelhaltig, für leichte Bearbeitung und Brechen) wird dafür verwendet. Andere Materialien sind zu zäh zum cracken. Schmiedepleuel weisen gegenüber Sinterpleueln ein besseres Verhältnis von Festigkeit zu Gewicht bei niedrigeren Kosten auf, jedoch ist die Gesenk-Herstellung sehr teuer und lohnt sich nur bei großen Serien. Bei Großmotoren werden die Pleuel geschmiedet oder gegossen. Bei Kleinserien werden die Pleuel spanend aus Metallstücken hergestellt.
Motorsport/Tuning:
Hier werden Vergütungsstähle oder Titanpleuel eingesetzt. Je nach Werkstoff und Vergütungszustand bevorzugt man das Schmieden als Vorformen (in einem Gesenk, das dem Bauteil in ein paar Schlägen die endgültige Form incl. Berbeitungszugabe vorgibt). Bei Vergütungsstählen, die im weichen Zustand zerspant werden, ist ein Anfertigen aus dem Vollen dank CNC Fräsmaschinen und Hartmetallbohrern kein Problem mehr.
Vergütungsstahl ist eine Stahlsorte, die in bestimmten thermisch behandelten Zuständen gut zerspanbar ist und durch Wärmebehandlungen durch und durch eine hohe Härte bis ca. 1300 N/mm2 bekommt, z.B.:
C70,
42CrMo4, 1.7225 (mittlere Zerspanbarkeit), weich ca. 700 N/mm², vergütet bei Wandstärken bis 16mm bis 1300 N/mm²
36CrNiMo4, 1.6511, Vergütungsstahl, zäh, Rohmaterial meist schon geschmiedet, wird durch thermisches Behandeln bereits aufgehärtet
30CrMoV9, 1.7707, Vergütungsstahl, Zugfestigkeiten vergütet über 1000 N/mm², auch für Nockenwellen,
31CrMoV9, 1.8519, Nitrierstahl, auch für Kurbelwellen oder Zahnräder, sehr ähnlich dem 1.7707
Die unteren drei Material güten gehören zu den AISI 4340 Stahlgüten, die wiederum zu den ASTM 29 gehören, die man für Pleuel verwenden kann. Das Material wird also nicht durch Zufügen von Stickstoff oder Kohlenstoff aufgehärtet, was z.B. für eine Lagerstelle nötig ist, sondern die komplette Zugfestigkeit wird durch Materialgefügeänderung bei der Wärmebehandlung umgewandelt. Geschliffen werden die Teile deshalb, weil sie sich bei der Wärmebehandlung in ihrer Form verziehen können und im "hochfesten" Zustand die Endgeometrie erzeugt werden muss.
Typische Materialien bei Rennsport Pleuel:
Stahl: AISI 4340
Aluminium: 7075 T6
Titan TiAl4V