Übersicht
Deckel FP4NC 1984
Deckel FP4NC 1997
Dialog Steuerung
Linux CNC
Mechanik
Ersatzteile/Reparatur
Wartung
Infos zu dieser Page
Kontakt
Datenschutzerklärung
Impressum
|
|
, DECKEL FP4 NC, Dialog 3, 1984
, Lackierung
, Geometrie
Seite 4, Aufbau
Aufbau
Lange genug hat die Deckel nun in der Ecke gestanden, dank neuer 100m2 Werkstatt kann ich nun im Winter arbeiten, darum wird Gas gegeben. Winter 2016/2017 wird der Maschinenfuß lackiert und der Rest der Lager bestellt. Und los geht es, erst mal an alle Steuergeräte Strom angeschlossen, damit die Akkus wieder fit werden.
Schon 2011 habe ich massig Spezialteile wie Abstreifer und Schürzen bei DMG bestellt. Viele der Spezialteile waren verhältnissmäßig preiswert, einige Zukaufteile aber Faktor 6 überteuert. So habe ich bei die Abdeckung 2810-3340 beim Hersteller statt für 370 Euro für 60 Euro bekommen. Die Lager bestelle ich ausnahmslos bei spezialisierten Lagerlieferanten.
Februar 2017
Kompletter Neuaufbau der Z-Achs Spindelführung. Dank Drehbank und Hydraulikpresse werden passende Stempel zum Einpressen der Lager angefertigt. Alle Lager an den Riemenscheiben sind original offen. Das hat den Nachteil, dass zusätzlich Fett auf den Riemen tropft, weshalb sich eine eklige schwarze Brühe bildet, vergleichbar mit Graphitfett. Ich baue moderne Lager mit Dichtscheiben ein.
Die Kegelradverzahnungen müssen fein eingestellt werden, minimalstes Spiel und trotzdem sehr leichtgängig.
Leider wie vermutet ist die Z-Spindelmutter defekt. Die Recherche nach bezahlbaren Ersatzteilen hält das Projekt wieder auf, die "ersten" Anlaufstellen verlangen etwas unrealistisch überhöhte Preise (für FAG oder SKF Lager habe ich bei Lagerhändlern nur 50-75% der Preise bezahlt). Auch die Anlaufscheibe der Z Achlagerung 2810-1123 war mir zu teuer. Ich lege einfach eine 5mm dicke Anlaufscheibe unter für 15 Statt 150 Euro. Dafür muß die Abdeckhülse etwas ausgedreht werden, aber eine Fräse ohne Drehmaschine ist ebenso wenig sinnvoll, wie ein Leben ohne Werkzeugmaschinen... Die 5mm weniger Verfahrweg in Z Richtung kann ich verschmerzen...
Generelles zur Z-Spindel: die X-und Y-Spindeln sind vorgespannt. Diese bekommen nur die Beschleunigungs- und Zerspanungskräfte zu spüren, der Verschleiss ist relativ gering. Bei der Z-Spindel lastet permanent eine Kraft durch den Kreuztisch und Winkeltisch von mehreren Tausend N statisch auf der Spindel. Aus dem Grund ist diese nicht vorgespannt, um den Verschleiss zu minimieren, aber nach einigen Jahren, auch bei wenig Benutzung ist die Mutter defekt. Ich besorge mir deshalb die Z Spindel gleich als Ersatzteil und bezahle für 2 Spindeleinheiten bei einem reellen Lieferanten weniger, als eine Spindel bei den OEM Lieferanten.
Einen Tag später ist die Y-Achse dran, das Handrad war eines der ersten Handlungen bei der Instandsetzung vor dem Umzug. Hier wird gerade der Motor angeschlossen und durch Öffnen der Motorbremse mit einem Labornetzteil das Spiel der Verzahnung am Handrad geprüft.
Die Spindel wurde durch Austausch der Kugeln und Reinigen überholt. Mutter und Spindel waren noch OK. Die Lagerung an Handrad, Spindel und des Zwischenstückes des Zahnriemens am Antriebmotor komplett erneuert.
März 2017: Getriebeschaltung
Wieder wie immer. Ein Blechdeckel des 12V Stellmotors war zerdengelt... Aber die Motoren laufen immer locker, die beiden Kugellager der Zahnradanlenkung sind wieder ungedichtete Versionen, bei mangelndem Ölwechsel und altem Kühlschmierstoff rosten diese Fest. In meinem Fall muss ich alle drei kleinen und drei großen Lager tauschen.
Böser hat es die Spindelkopfschmierung erwischt, durch das rostige Öl im Spindelbock war diese kleine Pumpe fest, mußte alles zerlegt und gängig gemacht werden. Witziger Weise brachte das Durchspülen mit dem dünnflüssigen WD40 nichts, erst mit synthetischen Motoröl löste sich die Rostbrühe und die Pumpe war wieder gängig. Danach konnte wieder das ISO-VG.. Hydrauliköl gepumpt werden, das im Getriebe zum Einsatz kommt.
April 2017: Lager
Noch fehlen Teile für die Endmontage, die Suche nach dem NU/RNU1011 mit der korrekten Rollenbreite (siehe Kapitel Ersatzteile) und das Warten auf die Sonderanfertigung der Z-Spindel soll im April zu ende gehen :-). Die Getriebemontage und Reinigung der Zahnräder geht nach zwei Feierabend Schraubaktionen zu Ende. Zwischen drin werden einige Kleinteile, der Schaltschrank lackiert, Betriebsstundenzähler eingebaut, sowie die seitlichen Maschinenabdeckungen repariert.
Mai 2017: Spindel
Anfang Mai ist die Z-Spindel da und der Kreuzschlitten kann montiert werden, sowie alle Messleisten. Also Endspurt. Mangels warmen Wetter werden die Seitenverkleidungen noch nicht lackiert.
Juni 2017: Lackierung und Endmontage
Endlich ist der Sommer da und die großflächigen Seitenteile können lackiert, sowie die Maschine komplett aufgebaut werden. Erste Tests ergeben, dass der Servoverstärker neu kalibriert werden muss (Offset und Driftabgleich). In der Betriebsart manuell kann die solide Bauweise aber schon genossen werden und ich arbeite mich in die Steuerung der Deckel endlich ein.
Im August hat die Maschine schon 22 Einschaltstunden und 0,5 Spindelstunden :-).
Kalkulation/Fazit
Maschinenkosten 5400 Euro
Ersatzteile 3700 Euro
Arbeitszeit selber
Summe 9100 Euro
Alle Verschleissteile wurden getauscht, selbst an der Elektronik wurden alle typischen Verschleissteile (Elkos, Sockel) getauscht, alle Teile komplett gereinigt und neu lackiert. Damit ist die FP4NC eine generalüberholte Maschine. Und jedes Teil der Maschine mehrmals in der Hand gehabt, da überrascht mich also nichts mehr, die habe ich nun im Griff :-).
Da ich mittlerweile einen neuen Arbeitskollegen habe, der sein bisheriges Berufsleben bei DMG in Pfronten verbracht hatte, bin ich inzwischen bestärkt, so eine alte Maschine zu pflegen. Alle Meister/Techniker, die ich inzwischen getroffen habe und die auf neuen Lineargeführten und alten Gleitbahngeführten Maschinen gearbeitet haben, sind von den "legendären" alten Maschinen begeistert. Diese bringen rein geometrisch die nöuml;tige Präzission und sind auch deutlich stabiler und schwingen weniger. Nicht umsonst werden selbst in 2017 noch alle Generationen der Deckel Maschinen im Werkzeugbau verwendet, wo es auf Präzission und nicht Taktzeiten oder Automatisierung ankommt.
März 2018: Erfahrung
Inzwischen hat die Deckel 11 Spindelstunden und einige Werkzeuge und Fräser in Betrieb. Mir ist aufgefallen, dass die Lager des Spindelmotors, die ich noch nicht getauscht habe, das Lauteste an der Maschine sind. :-)
Beim manuellen Fräsen macht sich die überholte Geometrie und die neue Z-Spindel insofern "negativ" bemerkbar, dass nach der Zustellung der Z-Achse und Eindrücken des Handrades durch die leichtgängige Mechanik alles um Zehntel mm runterrutscht, da die Bremse erst zeitlich verzögert in Aktion tritt (was bei X- oder Y-Achse keine Rolle spielt, da hier die Schwerkraft nicht wirkt). Da ich die Programmsperre nicht benötige, kommt hier ein Überbrückungsschalter für das Handrad rein. Nun stelle ich die Z-Achse auf µm zu, klemme manuell, schiebe dann das Handrad wieder ein und gebe die zusätzliche Klemmung wieder frei. So rutscht die Achse nicht mehr ab.
April 2018: Optimierung
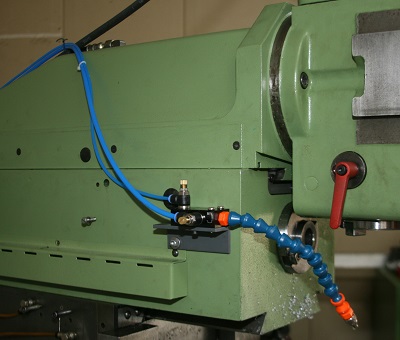 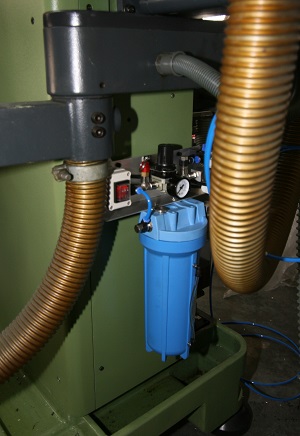
Nachdem ich schon einen HSS-E Fräser abgenutzt habe, wird ein Minimalmengenschmiersystem installiert, das spart viel Infrastruktur. Zu den Übungsstücken gehören auch Spannpratzen für den Schraubstock, um Rüstzeit zu sparen.
Viele der Signalgeber am Bedienpult funktionieren nur noch mangelhaft, ob das von der jahrelangen Garagenlagerung kommt, oder generell gealtert? Auf alle Fälle baue ich Rafi FS+22 Signalgeber mit LED's ein. Und schon gehen die Funktionen zuverlässig.
Nach 12 Wochen kommt der erste Mitutoyo Glasmaßstab, da zwei der Heidenhain Messköpfe defekt sind und eine Reparatur unverschämt teuer für diese minderwertigen Maßstäbe ist. Die neuen Mitutoyo sind hochgenau, maßkompatibel zu den LS903 und aktiv mit modernster Fotoelektrik. Die Eingangsstufen der NZP muss angepasst werden und zwar total unempfindlich gemacht werden. Das erhöht neben der Tatsache, dass die Mitutoyo's aktiv sind und einen niedrigen Ausgangswiderstand haben noch zusätzlich die Störunempfindlichkeit und damit die Genauigkeit. Nun ist die komplett neu aufgebaute Maschine erst fast 20h im Betrieb und man stellt doch wieder einen konstruktiven Mangel fest. Die Maßstäbe von X und Z Achse triefen von Bettbahnöl. Genau das sollte man den Maßstäben ersparen, wie mir ein DMG Techniker erklärt hatte. Leider sind die FP's hier mangelhaft, da die Position nicht wirklich von der Bahnführung abgeschirmt ist. Ein Grund, warum ich auch Mahos aus der Zeit habe und zu schätzen weis.
Ende April: Nun sind doch schon die beiden 520mm Mitutoyo Glasmaßstäbe da und die restlichen Zählerkarten können umgebaut werden. Nun kann ich wieder in allen Achsen Messen und mein 3D Tastkopf macht erst mal richtig Sinn :-).
Mai 2018:
Eine Abdeckung für die Horizontalspindel bei zurückgeschobener Vertikalspindel wird angefertigt, damit keine Späne in das Getriebe fallen.
Januar 2020:
Endlich nur Arbeiten, wenn auch noch manuell, 36 Spindellaufstunden und 264 Steuerungs- Einschaltstunden.
Januar 2021:
Der Umbau auf LinuxCNC beginnt, ansonsten 42 Spindellaufstunden und 340 Steuerungs- Einschaltstunden.
, DECKEL FP4 NC, Dialog 3, 1984
, Lackierung
, Geometrie
Seite 4, Aufbau
|